Общение в Клубе привело к неожиданному, странному и грустному выводу: мы совершенно не знаем КАК наши коллеги за океаном эксплуатируют свои промысловые коммуникации. Какие материалы труб они при этом используют, как налажено обслуживание, химизация, система картографии и т.д. и т.п.
Практически, НИКТО из членов клуба, даже те кто занимает должности ведущих руководителей, никогда не бывали на месторождениях Северной Америки. Более того, тема бизнесс-туризма вообще не приветствуется в российских компаниях (как изначано «порочная»)! А зря: имеенно в результате таких поездок можно и нужно узнавать и перенимать все лучшее, что практикуется у них, тем самым обеспечивая быстрое и эффективное развитие отечественной промышленности в любых направлениях (китайцы тому пример). К сожалению, сегодня осуществить это крайне сложно по понятным причинам.
Учитывая вышесказанное, имеет смысл обратиться к опыту прошлых лет, когда посещение российскими нефтяниками американских нефте-промыслов было еще возможно. Тем более, что основополагающие принципы подхода к вопросам эксплуатации и сохранения целостности коммуникаций остаются там неизменными по причине их экономической целесообразности.
Итак, начнем.
Примерно в 2010 году группа технических специалистов дочерних обществ крупной нефтяной Комании России, при содействии англо-русской фирмы-провайдера, посетила нефтяные месторождения Канады. Основной целью визита было изучение опыта эксплуатации промыловых трубопроводов, и, в случае подтверждения (как ожидалось) его эффективности — оценка возможности применения на крупном новом месторождении, а также в Компании в целом. В группу входили сотрудники централього и региональных управлений эксплуатации трубопроводов и специалисты корпоративного НИПИ. Группу сопровождали представители компании Confidence (UK) в статусе организатора визита и технического переводчика, представители федерального НИИ Канады.
Регион посещения — провинция Альберта. Первоначально планировалось посетить месторождения Аляски, но компания BP отказала в визите без обьяснения причин
Маршрут группы был следующим: самолетом «Москва-Франкфурт-Калгари», затем местными авиалиниями «Калгари — г.Кранде Прейри», оттуда наземным транспортом снова в Калгари, заезжая по пути на месторождения и нефтепромыслы местных нефтедобывающих компаний для ознакомления с обьектами трубопроводного транспорта и встречи с эксплуатирующими их специалистами.
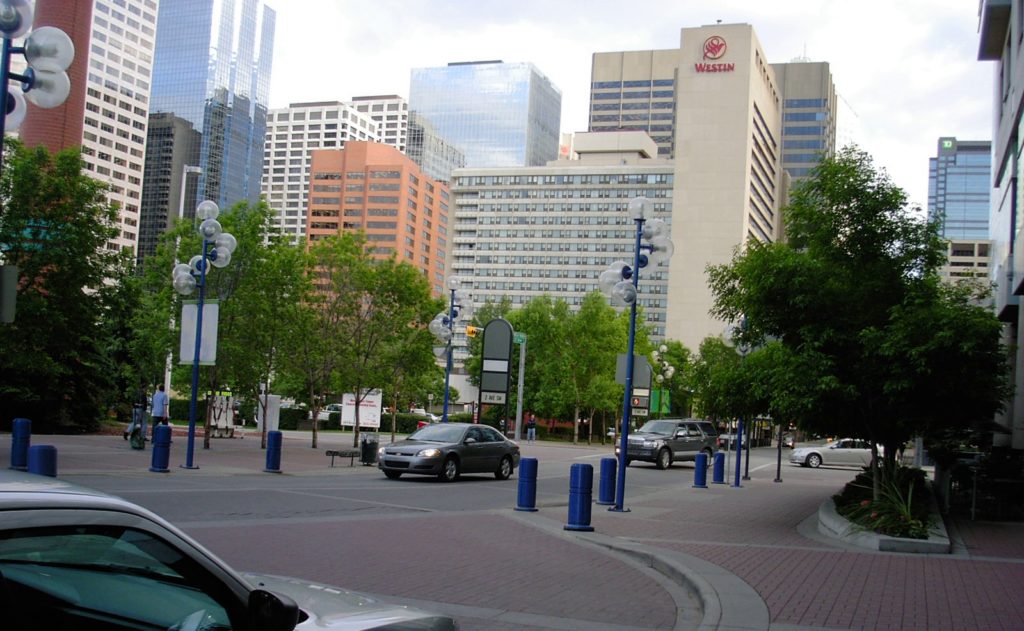
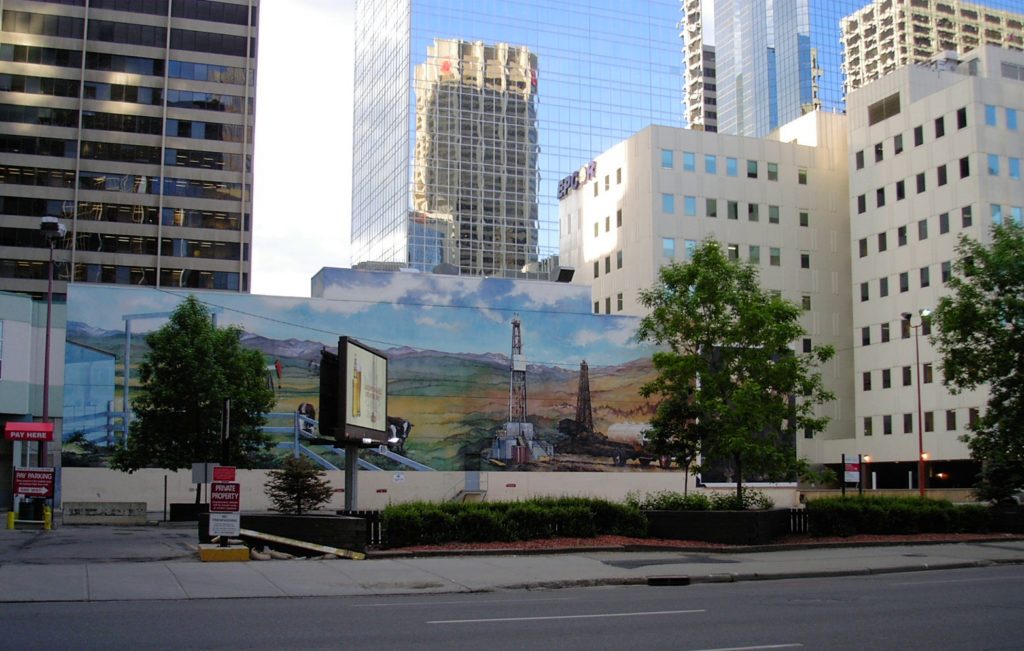
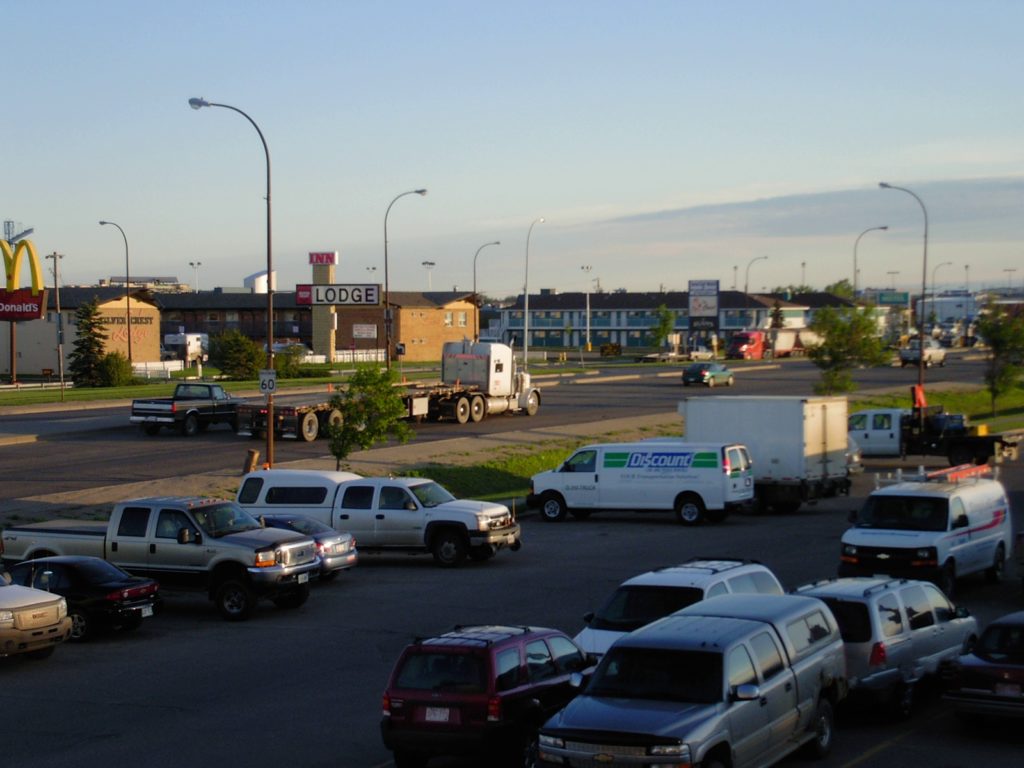
Следует сразу отметить доброжелательность и открытость канадских нефтяников, полное отсутстие высокомерия и амбиций, готовность показать и рассказать русским все, что их заинтересует. В этом смысле они очень похожи на наших специалистов и рабочих, которые трудятся непосредственно в регионах и на месторождениях. Вот их лица:
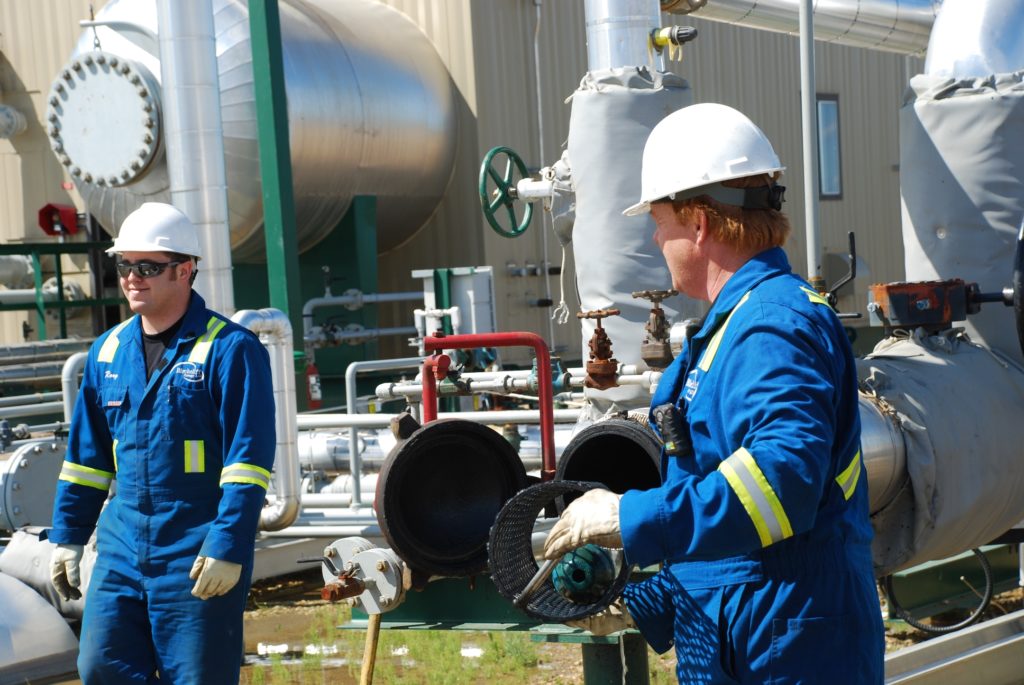
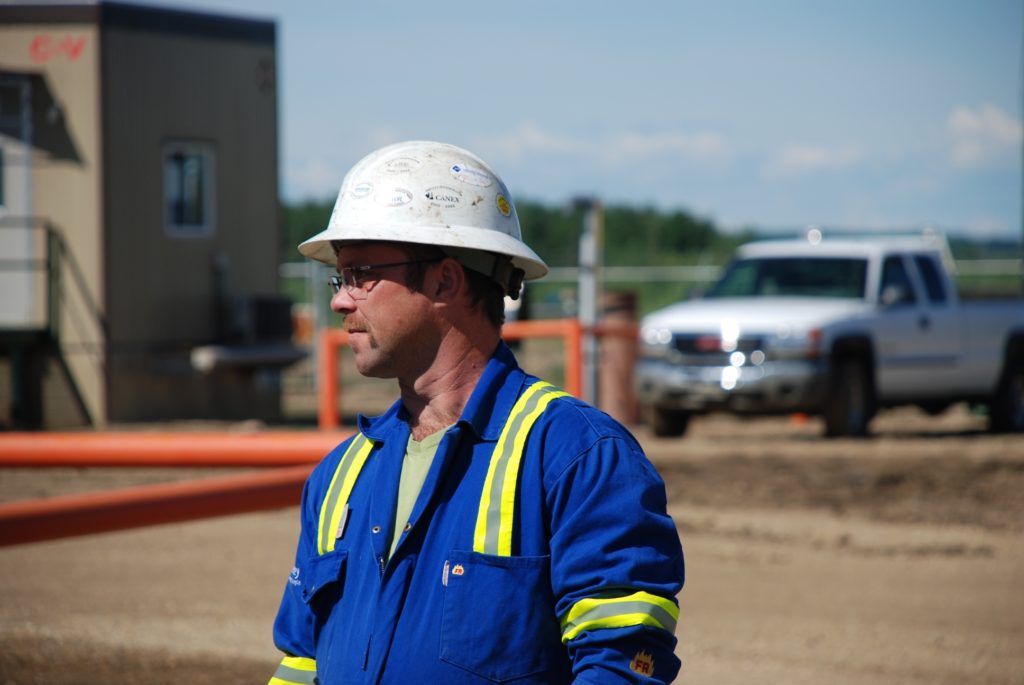
Одно, но принципиальное отличие от наших: работают спокойно, без нервов, ругани и суеты. Каждый знает свою задачу на смену. Никому ничего не надо повторять и, я думаю, проверять качество выполненной работы. Никаких ненужных планерок и совещаний без острой необходимости. Нужные для регламентных работ детали развозят по точкам на огромных пикапах, причем сами за рулем сидят, без специальных водителей. Обедают в ближайших мотелях и сидят там столько сколько сами пожелают. После работы собираются в местном баре смотреть ТВ и пить пиво (в меру!). По выходным с семьей отправляются на озёра отдыхать и ловить рыбу. В общем, говоря по-нашему: «Цветут и пахнут!». Но свое дело знают очень хорошо, работают на совесть, и, если надо, немедленно выезжают на обьект вне зависимости от дня и времени (за отдельную плату конечно, поэтому зря их не дергают). Что касается зарплаты — скромно молчали, но когда узнали про наш уровень, то со смехом высказались примерно так: «За такие деньги только до месторождения доехать и сразу, не выходя из машины, возвращаться домой!». Вот как-то так..
В период визита российская группа посетила месторождения северо-запада провинции Альберта: Simonette (добыча газа) компании Devon; Rycroft Piant (добыча газа и газоконденсата) компании Brichcliff Energy; Kaybob (добыча нефти) компании Trilogy Energy Trust; Pengrowth’s (добыча газоконденсата) компании Devon. На месторождениях были проведены брифинги со специалистами-инженерами по коррозии, кроме того в г. Calgary были проведены совещания со специалистами университета и сервисных компаний, занимающихся вопросами коррозии и обеспечения сохранности трубопроводов.
Провинция Альберта является основным нефтегазодобывающим районом Канады. Разработку месторождений ведут до 800 частных компаний. При этом, компании с участием государственного капитала, как в добыче, так и в транспортировке — отсутствуют.
СКВАЖИНЫ.
Кустовое бурение практически отсутствует. На месторождениях преобладают одиночные скважины механизированного фонда. Добыча осуществляется с использованием станков-качалок и ЭЦН. Обустройство скважинных площадок идентично нашему, но без обваловок.
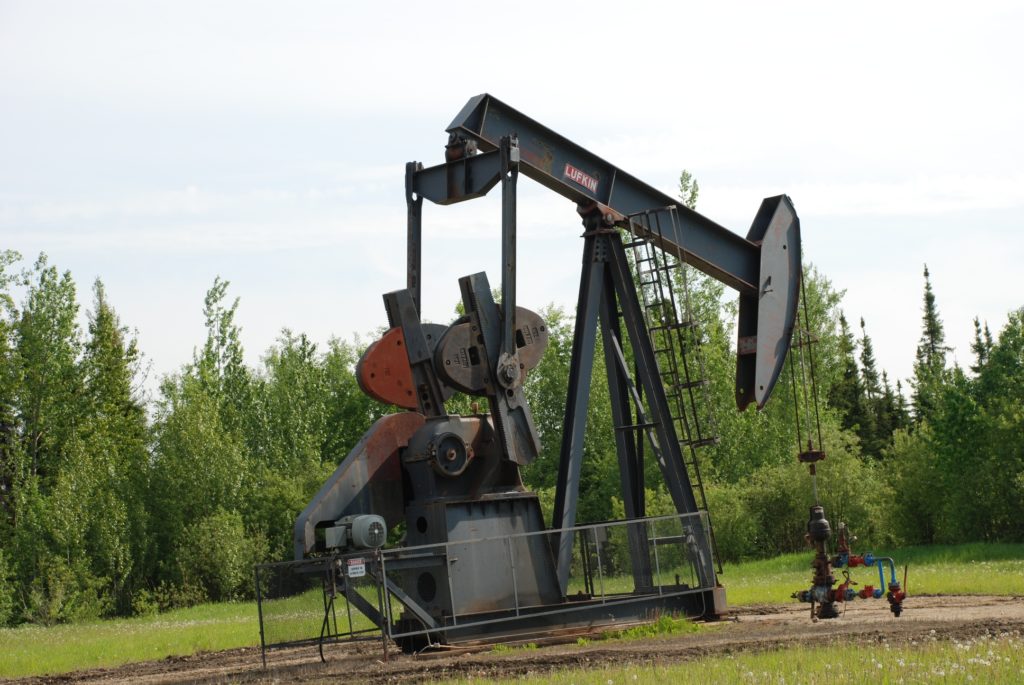
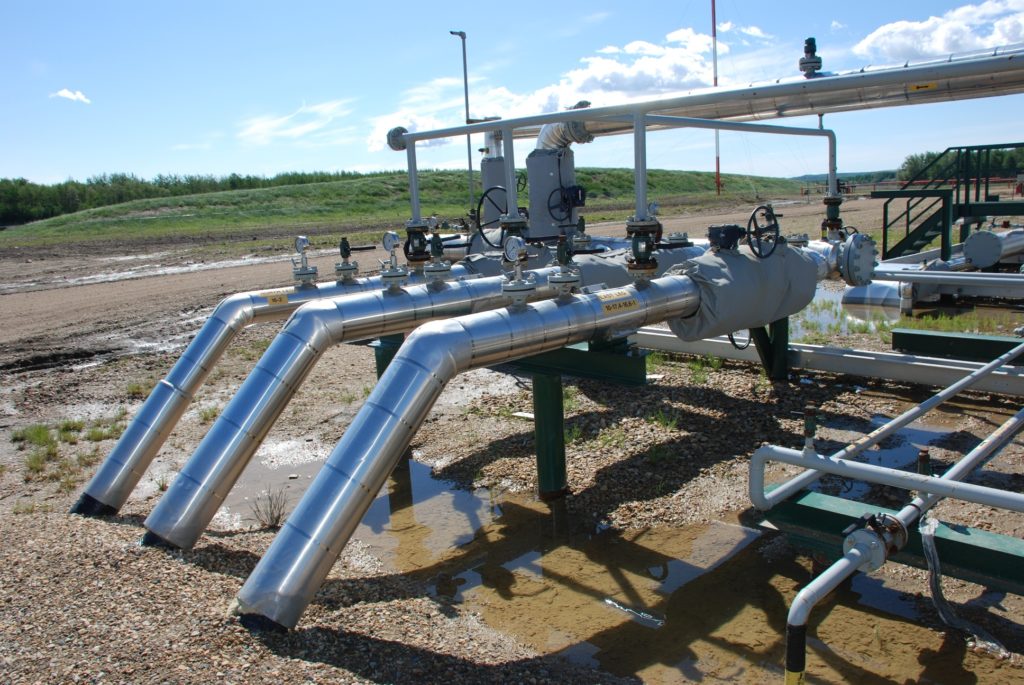
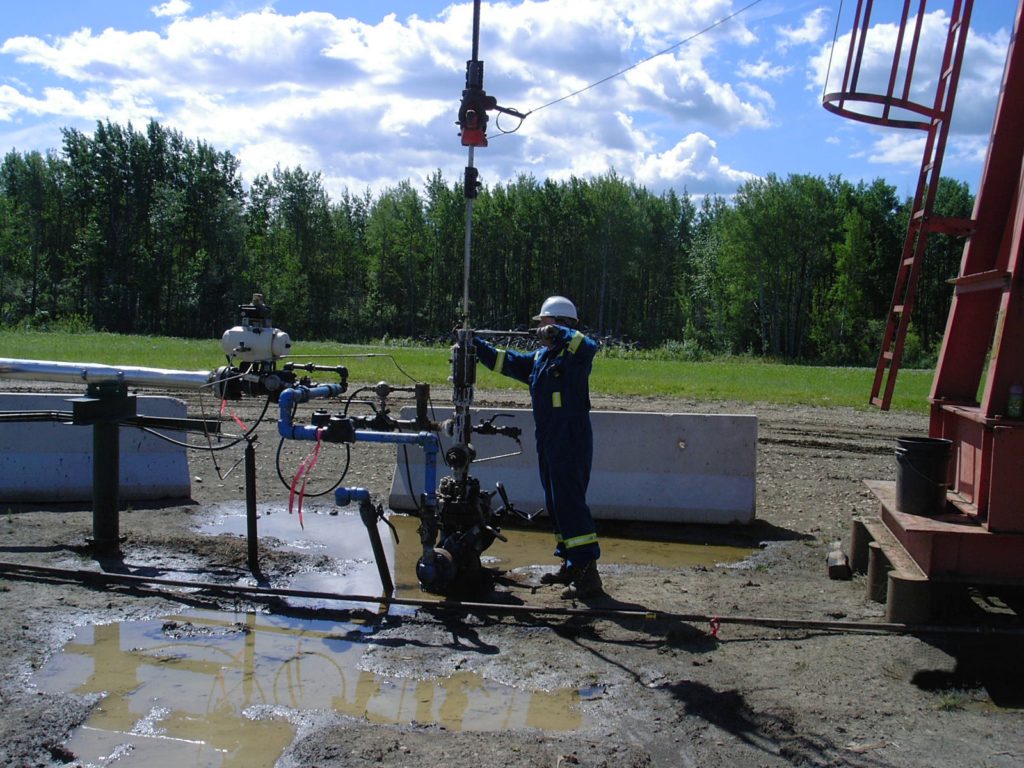
ТРУБОПРОВОДЫ
Применительно к нашей классификации трубопроводы в Канаде разделяют на магистральные (перекачивающие товарную продукцию) и сырой нефти (промысловые — от скважин до точек врезки в магистральные трубопроводы).
Общая протяженность действующих промысловых трубопроводов составляет 487 тыс.км. Удельная аварийность — 0,001 шт/км. т.е. в сравнении с нашими показателями — аварийность промысловых трубопроводов Канады практически отсутствует. Информация по коррозии трубопроводов не носит закрытый характер и не составляет коммерческой тайны. В связи с этим, в стране создана и активно действует ассоциация коррозионистов, обобщающая всю деятельность по безопасной эксплуатации трубопроводов.
Перекачка пластовых флюидов осуществляется так же, как и на наших месторождениях: от скважин по однотрубной системе. Никакого разделения потоков на газ, воду и нефть (как зачастую нам рассказывают) не существует: до пунктов приема по трубам перекачивается газо-водо-нефтяная смесь с теми-же рисками корозионных разрушений, что и у нас.
Трубы закупаются по американскому стандарту API-5L в двух исполнениях: обычном и для «кислых» сред, т.е. из низкоуглеродистой стали типа нашей ст.20 и стали низколегированной. Никаких особых марок сталей «повышенной корозионной стойкости» там не знают. Трубы из альтернативных неметаллических материалов встречаются, но в крайне ограниченном количестве, как дань каким-нибудь государственным программам. В общем трубопроводном фонде таких труб и одного процента не наберется.
Обобщая все увиденное, можно сказать следующее:
- Обустройство месторождений аналогичное;
- Технология добычи нефти и газа не отличается от нашей;
- Состав пластовых флюидов северо-запада провинции Альберта очень близок к нашей Западной Сибири (в попутном газе присутствуют и СО2 и H2S);
- Обводненность в районе 60-80%;
- Применятся стальные трубы без внутренних покрытий о которых местные нефтяники просто не знают;
- Марка стали в основном одна, и по составу близка к нашей ст.20;
- Трубы из композиных материалов применяются крайне редко и только для перекачки воды;
Т.е. все как у нас за одним исключением: аварийности трубопроводов практически нет. Наработка на отказ новых труб составвляет 25-30 лет (!).
Можно конечно рассуждать, что сталь у них лучше — чище — как говорят некоторые «специалисты». Возможно, но маловероятно: российские металлурги сегодня варят сталь не хуже, а порой даже лучше американских. На самом деле причина долголетия их трубопроводов кроется совсем в другом
Пойдем по порядку.
Точно так же, как и в США, в Канаде существует и активно работает Федеральное Управление безопасности трубопроводов. Именно оно делит всю территорию страны на зоны рисков от трубопроводов для населения, окружающей среды и предприятий. Именно оно рассматривает будущие трассы трубопроводов, и, в зависимости от их прохожденния через территории, назначает им уровни рисков. А дальше заказчик или принимает назначенные риски, или предлагает другой вариант трассы трубопровода.
Таким образом, там, за океаном, риски рассматриваются на государствеенном уровне, но не в отношении трубопровода, а в отношении территорий, через которые они проходят, с учетом всего, что на этих территориях находится: уровень заселенности, экология (реки, озера, флора, фауна), дороги, сторонние предприятия, заводы и т.п. Это, в конечном счете, и является основным фактором, обеспечивающим безаварийную длительную эксплуатацию трубопровода.
Учитывая присвоенные государством (в лице Федерального Управления безопасности трубопроводов) уровни рисков, владелец трубопровода разрабатывает то, что у нас называется «Декларацией безопасности», в которой перечисляются все технико-техноогические решения по локализации этих рисков. Документ никто из надорных органов не согласовывает, он просто подписывается владельцем и хранится у него в течение всей жизни трубопровода с корретировками при необходимости.
Здесь следует отметить, что в отличии от России, в Канаде федеральных надзорных органов на порядок больше, однако они никогда без особой необходимости не беспокоят владельца трубопровода. Но как говорят сами канадцы: «Если что-то случается, то инспекторы начинают нас разглядывать под увеличительным стеклом». Под этим «что-то» следует понимать любой порыв эксплуатирующегося трубопровода. И вот тогда уже для владельца наступают риски, вплоть до лишения лицензии на разработку месторождения. А это уже серьезно.
Таким образом, существует Декларация безопасности, которую составляет сам владелец, включая туда все то, что посчитает нужным, и свято исполняя свой-же документ, а уже инспектор (в случае аварии) смотрит: насколько мероприятия Декларации полны и соответствуют уровню назначенных государством рисков данного трубопровода. На фоне вышеизложенного никому и в голову не приходит экономить на антикорозионных мероприятиях, именно поэтому компании выбирают самое эффективное — защиту трубопровода ингибитором коррозии.
То что ингибирование существенно снижает фоновую скорость коррозии нам известно, но представляет интерес то, КАК они это делают.
Когда-то в России существовала нефтяная компания под названием «ЮКОС». Не берусь её обсужать, но вот то, что там начинали делать специалисты службы эксплуатации рубопроводов заслуживает самого пристального внимания. Дело в том, что это начинание на 100% сотвествует существуюшей сегодня практике нефтяников Северной Америки. Именно эта комплексная технология позволяет им там, за океаном, эксплуатировать без порывов трубопроводы по 25-30ле, вне зависимости от сталей и агрессивности флюидов. В ЮКОСе она называлась ЧИК, что означает Чистка-Ингибирование-Контроль. Бизируется она на известном приницпе защиты стали путем создания на её поверхности микропленки. Но при этом принципиальным моментом (моменом истины, если угодно!) является то, что эта пленка должна образовываться на преодварительно очищенной от отложений внутренней поверхности трубы. Нет эффекта только от ингибирования, и нет эффекта только от очистки. В последнем случае процесс коррозии даже ускоряется. Именно этим обстоятельством обьясняется, в частности, многочисленные случаи порывов трубопроводов после проведения внутритрубной диагностики, т.е. очистки внутренней полости трубы без её последующей защиты. К сожалению, Проект «ЧИК» внедрить в ЮКОСе не успели: Компания прекратила свое существование. Кто родоначальник этой комплексной технологии защиты — сказать сложно. Вполне вероятно, что иностранные топ-менеджеры ЮКОСа привнесли её. Но это и не важно сейчас.
Коллеги в Канаде поступают следующим образом:
- Сеть коммуникаций месторождния передается в обслуживание на длительный срок (не менее 5 лет) крупному химическому концерну. Вместе с тем этому же концерну вменяется и финансовая ответственность за сохранность трубопроводов. Учитывая это, а также то, что фронт работ гарантирован на несколько лет вперед, химики подбирают реагент наиболее оптимальный по критериям: эффективность не менее 90%, и цена не более $$$ за тонну. При этом цена фиксируется на весь срок контракта. Ежегодных тендеров не проводят.
- Расчетным путем определяются точки установки камер пуска-приема очистных устройств.
- Расчетным путем, исходя из «пробковой» технологии закачки, определяется расход реагента и его годовая потребность.
- Расчетным путем определяется периодичность очистки участка трубопровода и подачи туда реагента-ингибитора коррозии. Критериями является скорость потока и продолжительность эффекта последействия реагента.
- В конце каждого участка устанавливается электронный узел контроля коррозии для оценки остаточного количества ингибитора в перекачиваемой среде. Никто и никогда не использует там УКК для оценки эффективности стали, посколько ни гравиметрия, ни электроника никак не коррелируют с реальной скоростью разрушения металла труб.
- С определенной периодичностью оператор производит пропуск полиуретановых очистных поршней, между которыми закачивантся «пачка» ингибитора коррозии в необходимом обьеме (задний поршень имеет пазы для пропуска реагента).
- Специалисты — химики контролируют и регулируют наличие ингибитора в емкостях, его качество, остаточное количество в конце участка и обьем закачки (дозировку). Принятые у нас технологии постоянной подачи реагента через БРХ там не используются в силу очень высокого расхода (=затрат) и это подтверждается расчетами.
Ниже представлены фотоматериалы, иллюстрирующие процесс очистки и ингибиторной защиты.
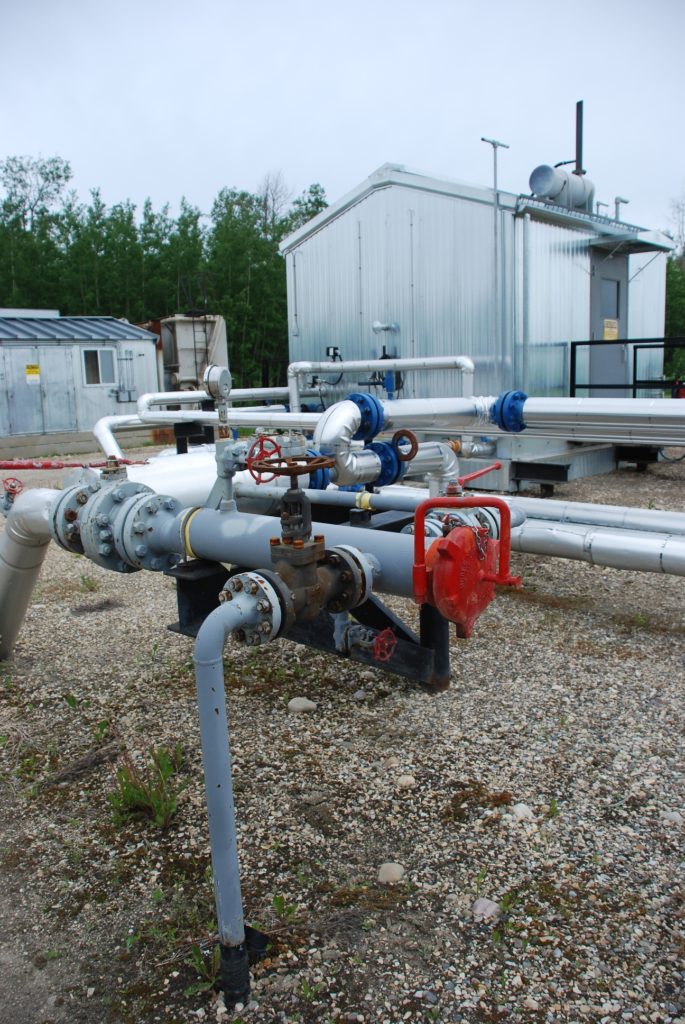
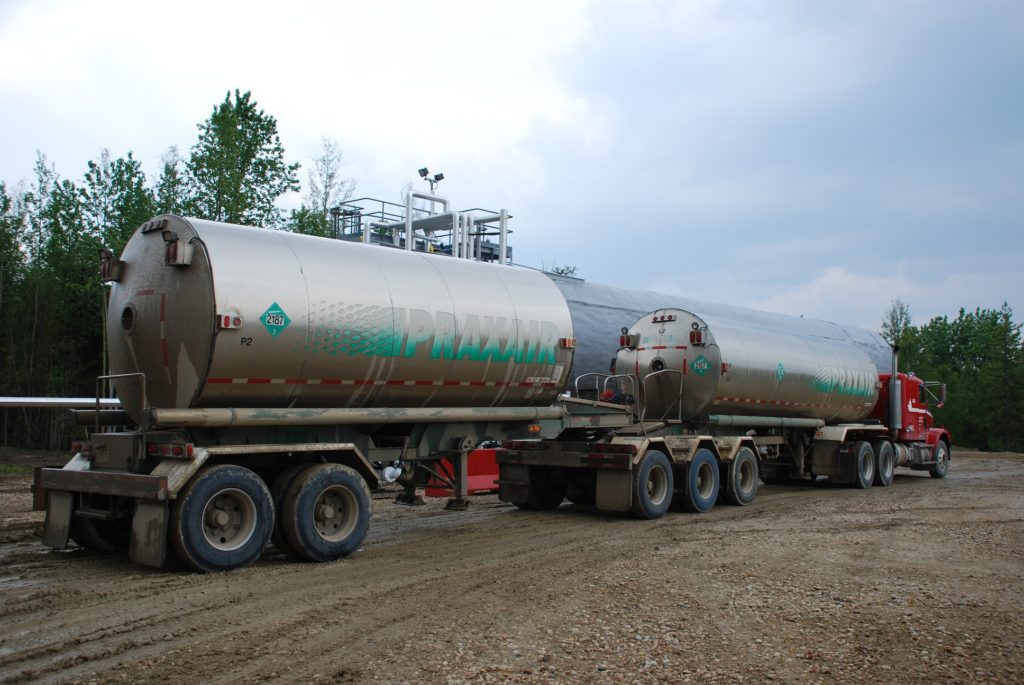
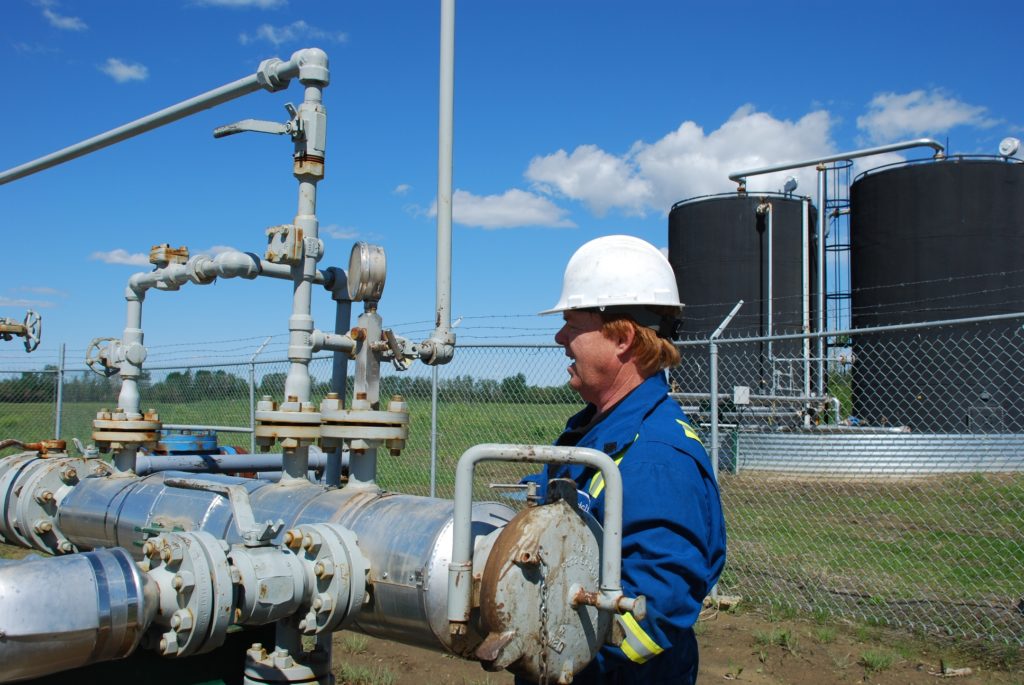
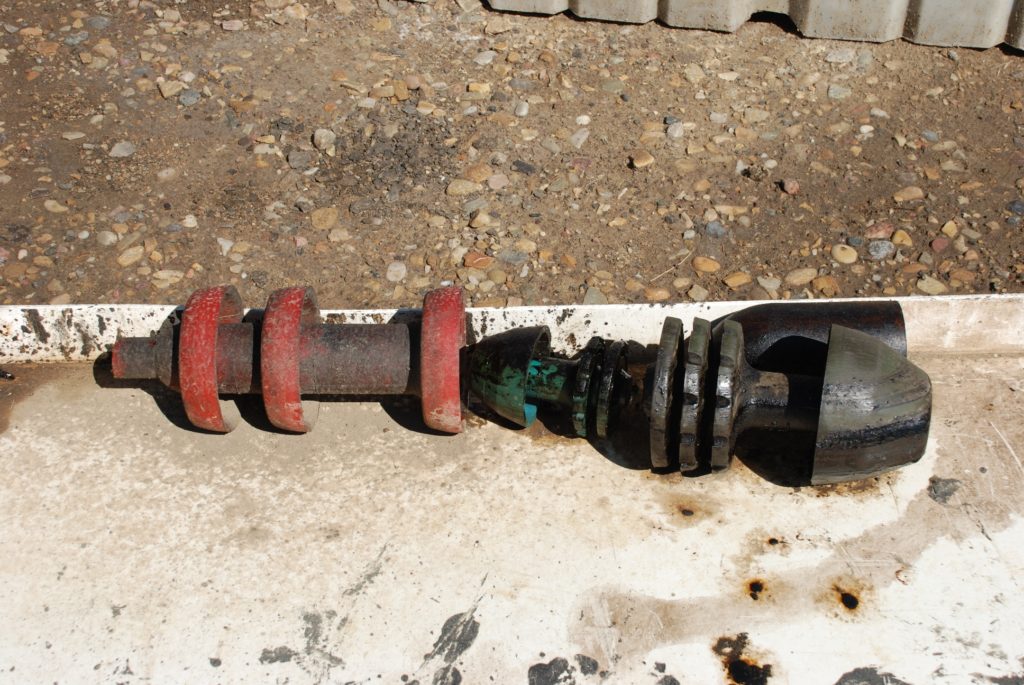
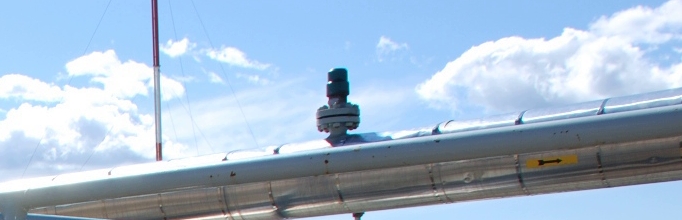
Возникает естественный вопрос: «Что нам мешает работать по той же схеме?!» и «Почему мы так настойчиво стремимся получить «вечные» трубы, не обращая никакого внимания на то, как работает весь остальной мир в этой области?». Ответы есть. Вот ключевые из них:
- в России компаниям выгоднее вкладывать деньги в капитальные затраты нежели в операционные.
- Отсутствует государственная структура, конкретно направленная на обеспечение безопасной эксплуатации трубороводов.
- Вопросы экологической безопасности не являются для компаний приоритетными. Нам не известен ни один случай лишения лицензии на разработку месторождения за порывы коммункаций и нанесение вреда окружающей среде.
- Практически во всех нефтяных компаниях существует требование проведения ежегодных тендеров на все и вся. Вопрос контрактации на длительный (5 и более лет) вообще не стоит. Естественно, что подрядчик никак не заинтересован в качественной работе поскольку не знает что будет завтра. Тендеры в российской действительности вообще приносят больше вреда чем пользы, но это отдельный разговор.
- На большинстве трубопроводов отсутствуют камеры пуска-приема очистных устройств. Как правило их устанавливают на трубах большого диаметра (более 500мм) тогда как промысловые коммуникации это трубороводы малого и среднего диаметра. Между тем, существует отечественный производитель, давно освоивший производство малогабаритных камер пуска-приема ОУ.
- Ингибиторы коррозии закачиваются по технологии постоянной дозировки, требующей наличие специального блока реагентного хозяйства (БРХ). Считается, что только такая технология эффективна, но это далеко не так.
- Комплексное применение очистки с ингибированием практически не применяется.
- Сотрудникам служб эксплуатации трубопроводов не знакома мировая практика защиты промысловых трубопроводов. Каждый использует свой подход, в силу своего профессионального опыта и знаний. Обмен информацией в условиях российского рынка крайне затруднен в связи с грифом «секретности».
Мы идем по пути совершенствования труб и покрытий. Но это тупиковый путь хотя бы потому, что он ведет к взаимоисключающим решениям: повышение корозионной стойкости трубопроводной продукции вызывает повышение её стоимости, но дорогие трубы не интересны покупателю. Применение покрытий и неметаллических материалов так же связано с высокой ценой, а кроме того с проблемами при строительстве, эксплуатации и диагностированию.
Именно поэтому мы рассказали о том КАК работают наши коллеги-нефтники в Канаде и ПОЧЕМУ они спокойно эксплуатируют трубы из стали типа 20 без порывов и аварий до 30 лет, тогда как у нас аналогичные трубы зачастую не выдерживают и года эксплуатации.
В принципе все просто. Успехов вам!
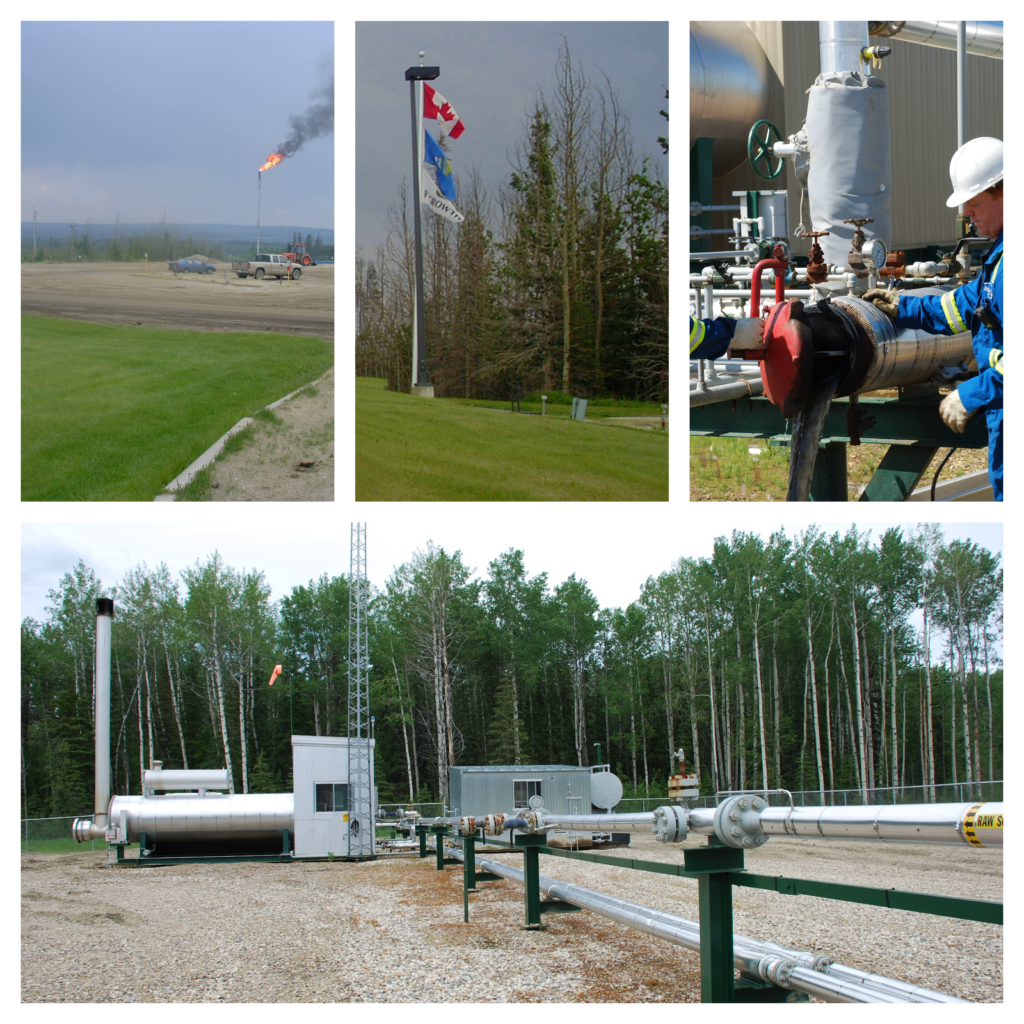